AUTOMATED LASER SYSTEMS FOR MANUFACTURING

Laser automation is the process of using laser technology to improve industrial processes. Therefore, applications such as laser cutting and laser welding are examples of capabilities within this automation area. This type of automation can enhance efficiency and precision for different kinds of industries.
Automated laser applications may be based on either motion systems, robotics or a combination of both. The laser is usually built in a cell for safety purposes, and then integrated with other technologies such as Vision to meet different needs. Once programmed for a specific purpose, a laser cell can execute a high-quality and accurate work within seconds.
THINKING ABOUT LASER SOLUTIONS?
Share your laser automation needs now by completing our informational form
Benefits of Laser Automation
Robotic Laser Integration
Often robotic laser systems are the most optimum solution for cutting and certain types of welding. Optimal integration of these systems requires special expertise and BOS is an industry leader when it comes to designing and implementing these cutting edge interfaces.
Laser Safety
Safety is always an issue with laser automation. Our laser safety officer and design team will ensure your system is certified safe, all the way up to and including Class 1 laser enclosures that exceed the demands of laser safety standards. We can build standalone marking and welding systems, right up to enclosures with various types of automatic doors and part loading.
Laser Process Development
If you’re not sure if lasers are right for your production task, we can work with you to get the answers you need. From initial feasibility reviews, to functional testing and complete process development engineering studies, we can provide you with the right data to make informed decisions on automated laser production.
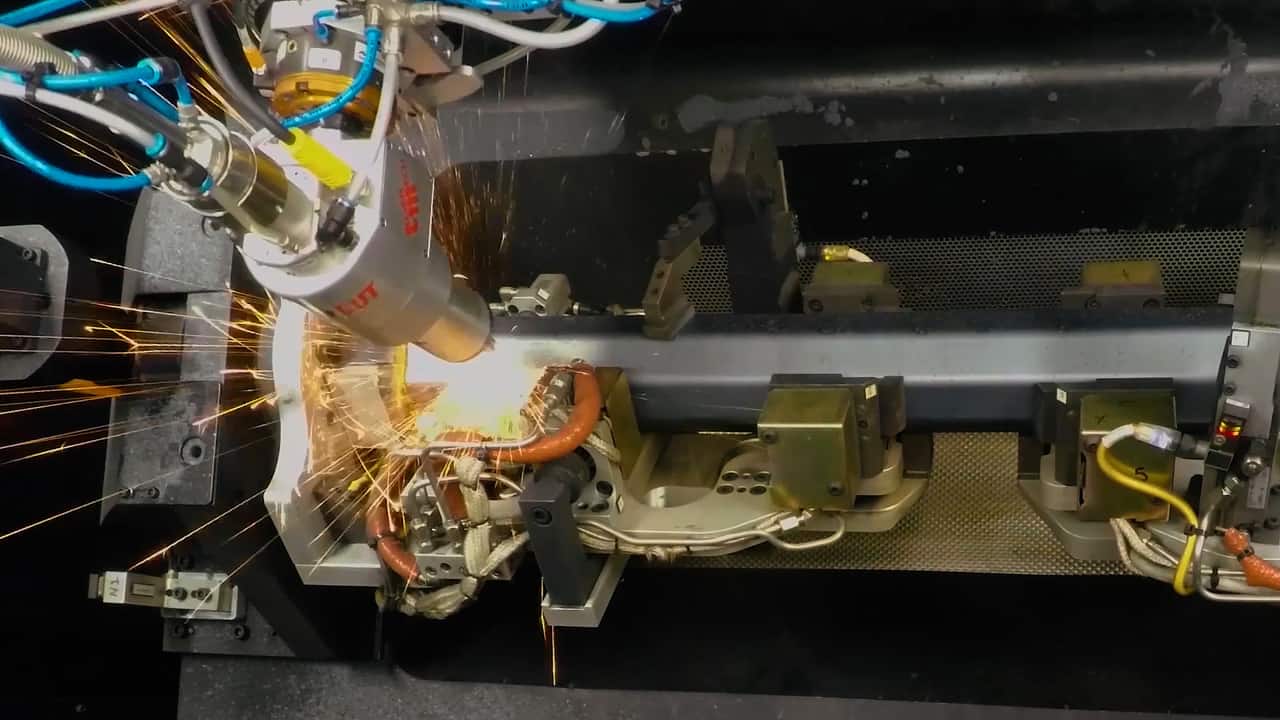
BOS Custom Laser Automation Solutions
From welding and cutting, to marking and surface treatment, add BOS expertise to the process development of your laser based automation application.
Laser Welding
If you require laser welding, we’ve got the automation solution for you. Regardless of the industry your company fits in, we have the experience to provide you with the right laser welding robotics and systems to make your process a success.
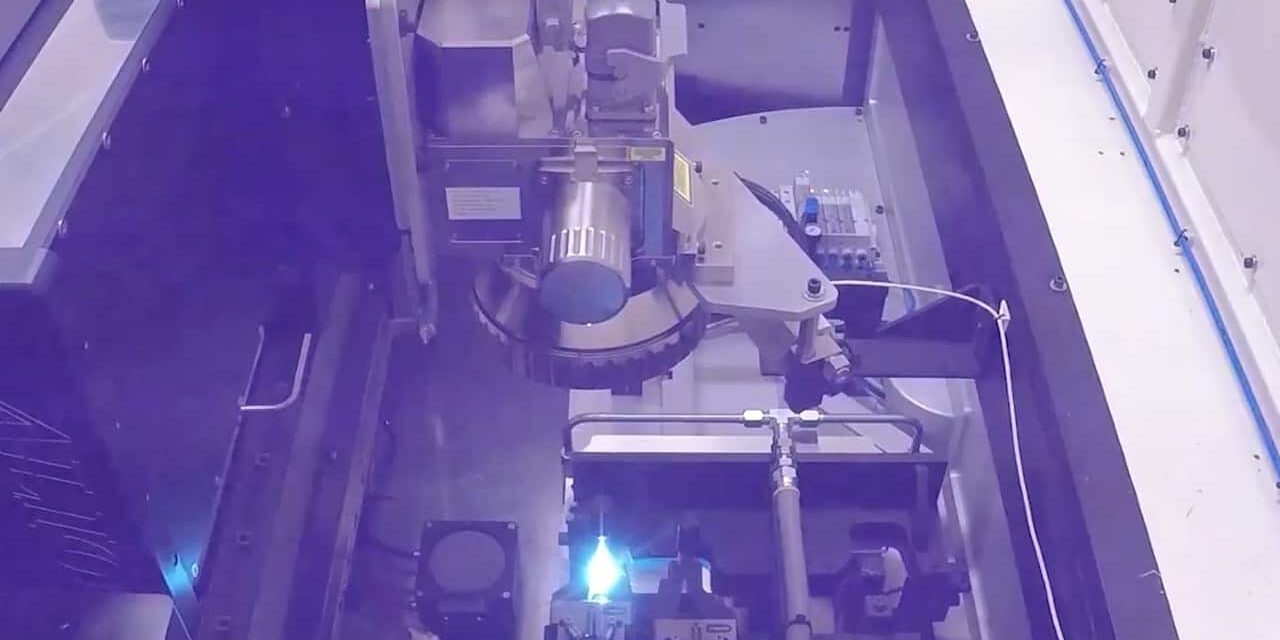
Laser Cutting
We can design and create automated lasers for cutting nearly any product type, from certain plastics and membranes to most types of metals. If your process requires the use of laser cutting robots or CNC motion systems, we can engineer and install the right solution for your job.
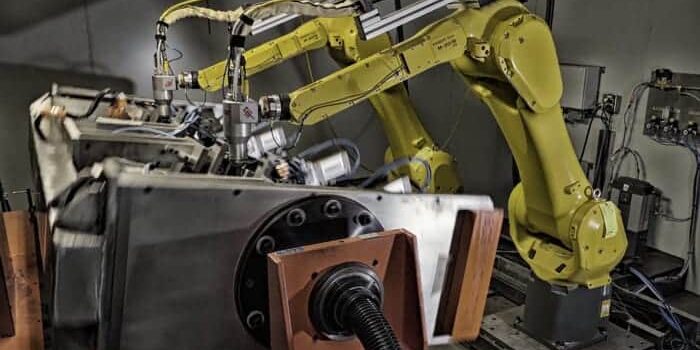
Advanced Manufacturing Solutions
Not sure where to begin? We have proven, modular designs to help get you started. If you need something a bit different, no problem, our experts are available to customize it just for you.
Check out our laser cells for industrial laser cutting or welding:
L-R
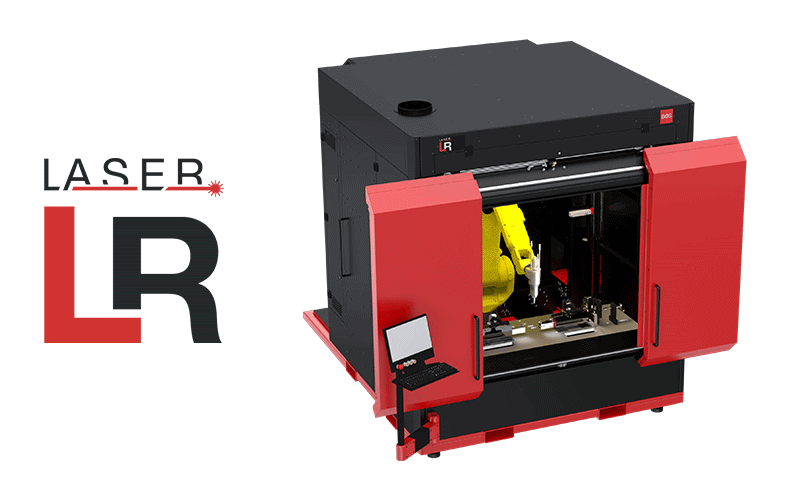
L-MS
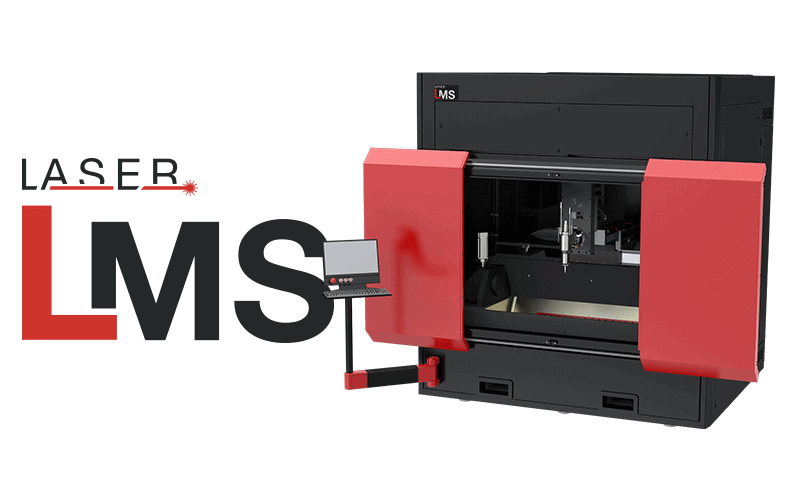
Battery Cooling Plate Laser Welding for Electric Vehicles (EVs)
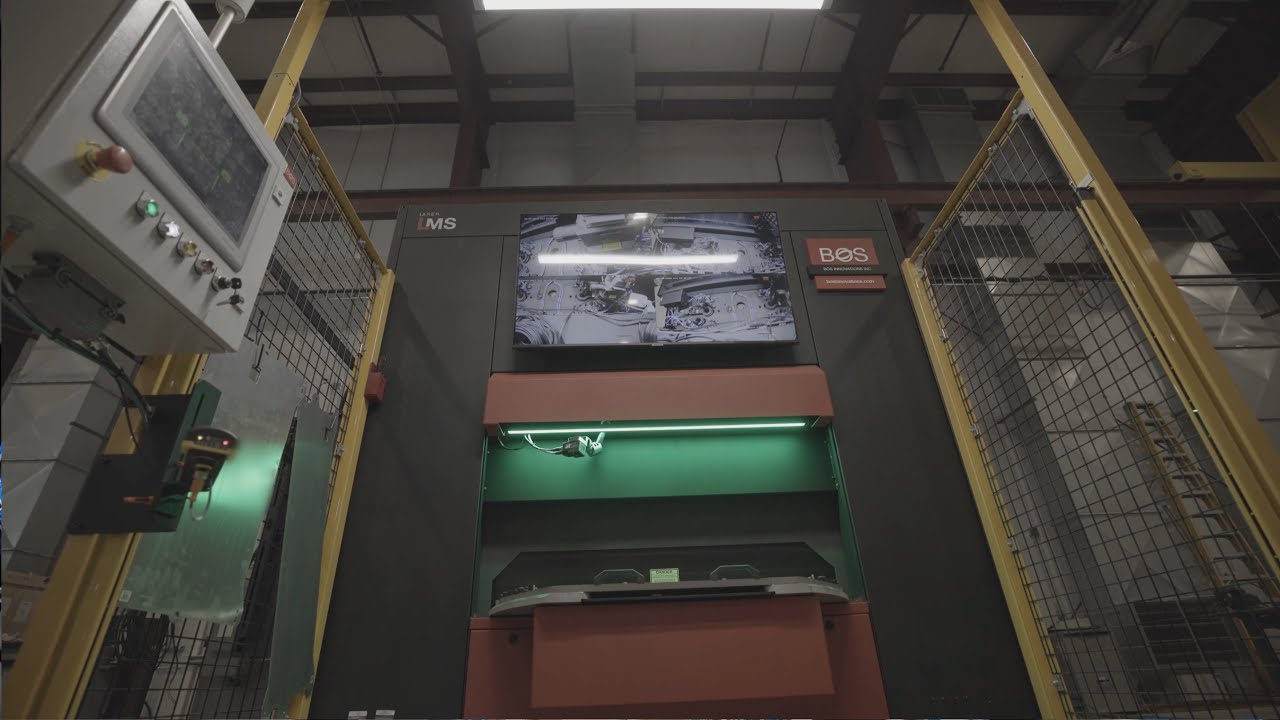
Our customer required aluminum components to be welded together with precision tolerances to assemble battery cold plates for an OEM manufacturer of EVs.
There were two (2) different part variants. The machine would be manually tended (loaded/unloaded) by operators and had to achieve a maximum part-to-part cycle time of 20 seconds (including operator time).
Traceability of weld quality at the finished assembly level was required. The completed assembly had to pass leak testing.
After performing a feasibility study for the customer, BOS determined that the most precise weld process for their parts would be successfully achieved by an L-MS laser cell. The machine would be powered by a 2kW fiber laser and remote welding head from IPG to be deployed on a 3-axis linear motion system with direct drive encoders and CNC motion control. The circular welding process required coordinated motion of the remote welding head and the precise motion system.
The machine utilized quick-change tooling and a combination of mechanical and digital poka-yokes for part variant control.
An automatic start-up verification procedure was programmed, utilizing a laser beam power meter, to validate laser quality at the start and end of every production shift. Each part received a barcode scan and an impact mark for traceability.
The commissioned laser cell achieved its performance, quality, and safety requirements, including its 20 second part-to-part cycle time for both welding processes (including operator load/unload time). Additionally, by having conducted a thorough feasibility study on the customer’s original process, BOS was able to reduce unnecessary overlap joints decreasing from four to a single point of failure on each weld which allowed the system to precisely detect imperfections as soon as they occur.
10kW Laser Welding for Hydraulic Cylinder Tubes
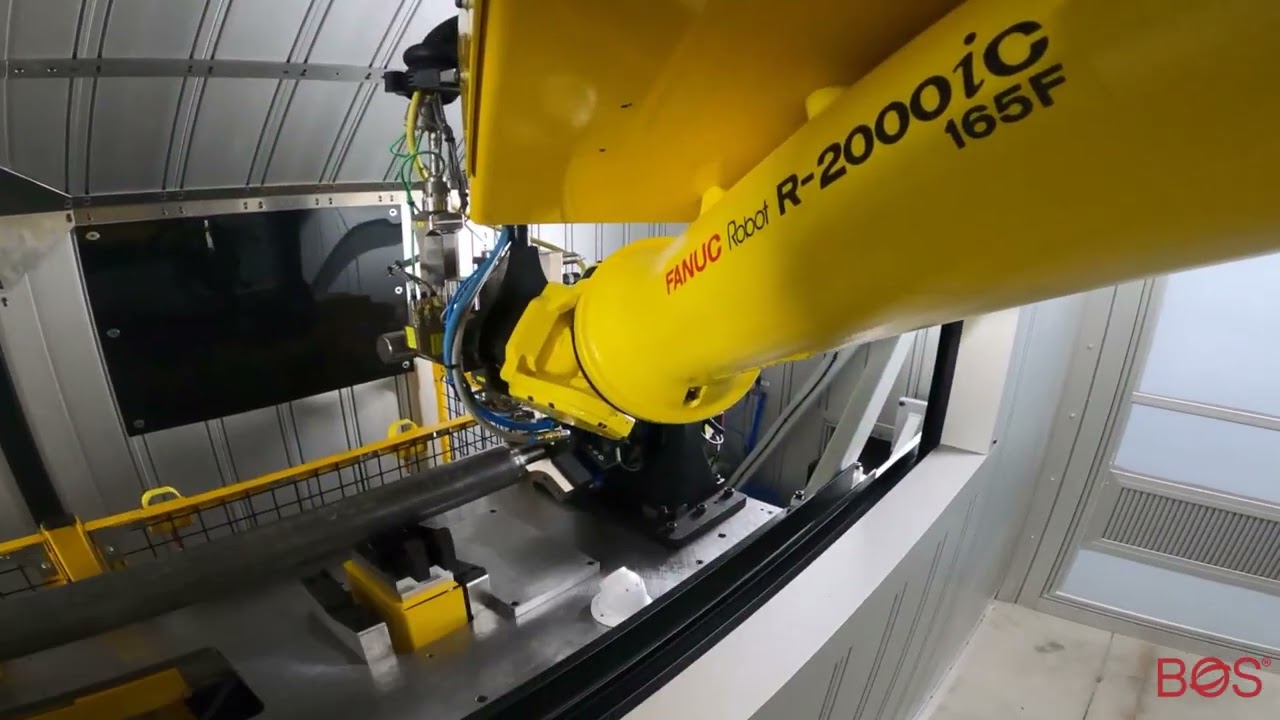
Our customer required a laser welding cell to produce sections of telescopic cylinders for various applications. This new machine would be implemented in the context of a new flexible manufacturing system within the customer’s plant.
There were five (5) different part variants with wall thickness of welding joint ranging from 0.25inch to 0.5inch. The machine would be designed to accommodate both automated and manual loading of the components.
Laser welding process would be performed by an IPG 10kW fiber laser system mounted to a FANUC R-2000iC/165F robot. Weld quality would be monitored by IPG LDD-700 system integrated to their D50 wobble welding head. Cameras should be strategically placed inside the cell to allow for real-time monitoring while doors are closed.
A BOS L-R cell was built with a class 1 laser enclosure and double sliding doors on each side to allow part loading on one side while the laser welds on the other side. Each of the doors were interlocked and the safety PLC ensures that the laser is always contained within the laser guarding while it is firing. Manual and fully automated modes were accommodated on the equipment for the customer to switch between human and robotic loading/unloading as needed.
The 10kW fiber laser and the LDD-700 weld monitoring systems from IPG were deployed on the 6-axis FANUC industrial robot. This allows the welding laser and the measurement beam to be fired through the same optics for direct, geometric measurement of weld penetration.
A tailstock that applies force and presses the part for welding was mounted to a linear servo slide allowing the cell to be quickly adjusted for the various part lengths without the need for tooling changeover.
Proximity Smart Support was installed on the machine for quick, remote support from our team of specialists when needed. It also allows the operation to be monitored through an HD screen installed right outside the cell that displays internal images from 4 different perspectives.
The turnkey L-R robotic laser weld cell achieved its performance, quality, and safety requirements becoming a flexible piece of equipment for our customer due to its ability to produce different part types.
The transition to laser welding resulted in a substantial increase in weld speed as well as eliminating the need for filler wire as required from the previous weld process.
The LDD monitoring system collected data to complete 100% in-line inspection of seam position, keyhole depth and finished weld profile, providing real-time results without destroying the part which translates to both more profitability and sustainability to the customer.
Finally, Proximity Smart Support has made it possible for the customer to achieve a low downtime due to the remote, expert support available for them through the system.
Robotic Laser Cutting Cell for Exhaust Tubes
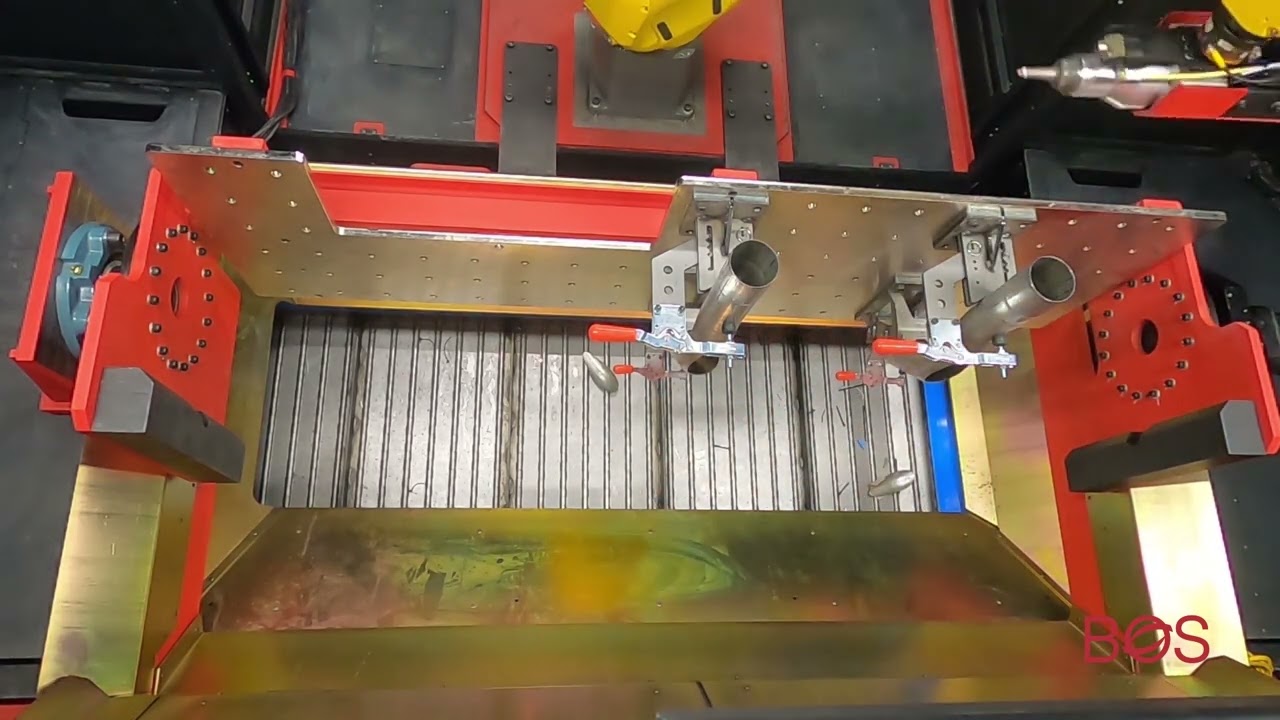
Our customer required an automated system capable of performing complex laser cutting tasks such as a large oval hole.
The laser cell would be manually tended (loaded/unloaded) for this high mix/low volume production of tubes for premium aftermarket exhaust systems, and the cutting scraps should be automatically carried out of the workcell to a scrap bin.
BOS designed and built a BOS L-R workcell comprised of a Fanuc M20iB Laser cutting robot with a Laser Mechanisms FiberCUT ST cutting head and a 2kW fiber laser from IPG for this customer. This L-R cell also features a dual trunnion turntable with manual change fixtures for part positioning, CAD to path programming with FANUC WeldPRO software as well as a scrap conveyor and an operator load station. Proximity Smart Support was installed to the machine for quick, remote support from our team of specialists when needed.
The coordinated motion of the 6-axis laser cutting robot and the 3-axis dual trunnion turntable have successfully made this L-R laser cell a flexible piece of equipment for our customer as it can be programmed to multiple part types through its low-cost, quick change manual fixtures. Since its installation, the system has been expanded from 6 to more than 250 part variations while maintaining its precision in laser cutting. Additionally, by having integrated several laser cells in the past, BOS has streamlined the integration costs of these systems and is able to pass these savings on to the end customer. Finally, Proximity Smart Support has made it possible for the customer to achieve a low downtime due to the remote, expert support available for them through the system.
Precision 3-Axis CNC Laser Cutting for Truck Side Step Rails
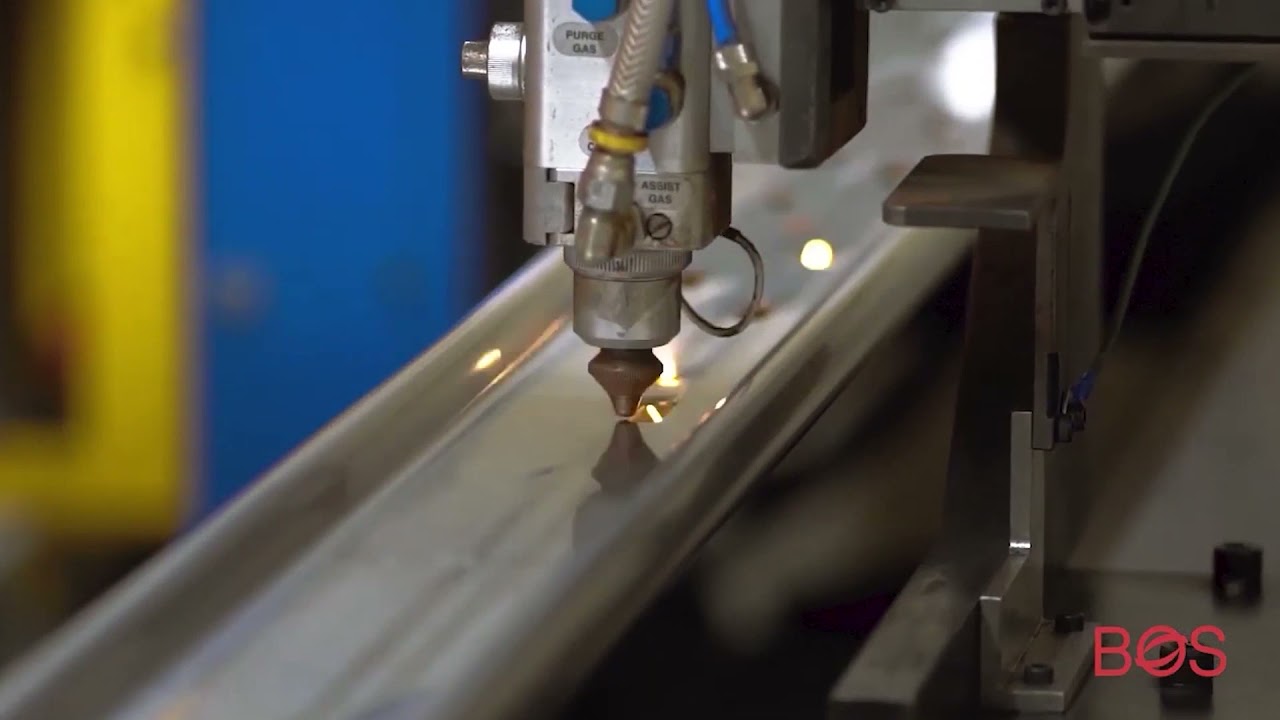
Our customer required 36 holes with tight tolerances to be laser cut in stainless steel rails to create side steps for an OEM truck program. The ends of each rail also needed to be cut off squarely and without any burrs to accommodate the insertion of a plastic end cap at a downstream process.
There were four (4) different part variants for various wheelbases and cab lengths. The laser cell was to be robotically tended and had to achieve a part to part cycle time of 90 seconds or less (including load/unload).
To achieve the cycle time and precision required, a 2kW fiber laser from IPG and a cutting head from Laser Mechanisms were deployed on a 3-axis linear motion system with direct drive encoders and Beckhoff CNC motion control.
BOS designed a rotisserie-style trunnion tooling to grip the rail from inside and utilized coordinated motion to cut each of the holes and complete the end cuts.
The integrated control system allowed for part variant changeover at the push of a button (no manual change-out required).
The commissioned laser cell achieved its performance, quality, and safety requirements, including its 90 second part to part cycle time.
Precision 5-Axis CNC Laser Cutting for Tier 1 Automotive Manufacturer

Our customer required 6 to 12 holes (variant dependent) with tight tolerances to be laser cut in octagonal steel tubes with variable wall thickness to create a component for an OEM automotive program. One end of each tube needed to be cut off at a 21.5 degree angle.
There were two (2) different part variants. The laser cell was to be robotically tended and had to achieve a part to part cycle time of 40 seconds or less (including load/unload).
To achieve the cycle time and precision required, 5 axes of CNC motion control were coordinated with a trunnion positioner. A 1kW fiber laser was deployed on a rotary cutting head to allow for the range of motion required to complete the 21.5 degree and cuts.
Complex tooling was required that could slide and re-datum the part mid-process. The sequencing could not affect the repeatability of the cutting process.
Laser focal length and cutting power were optimized throughout the process to accommodate for the variable wall thickness of the octagonal tube.
The integrated control system allowed for part variant changeover at the push of a button (no manual change-out required).
The commissioned laser cell achieved its performance, quality, and safety requirements, including its 40 second part to part cycle time.
This was one of the first pre-engineered L-MS laser cells integrated for a customer.
Laser and Saw Cutting for Roof Rails Manufacturing
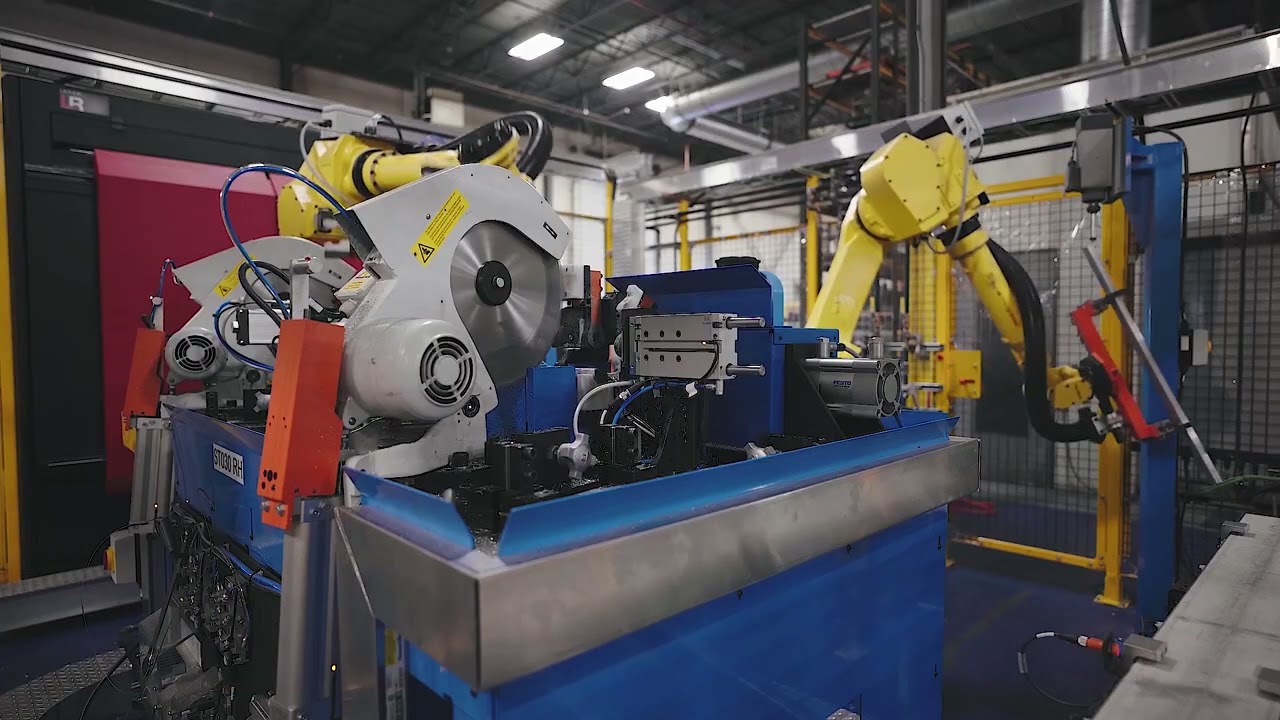
Our customer required a workcell capable of producing aluminum roof rails for an OEM automotive program.
There were two (2) different part variants: LH and RH. The workcell would be manually tended (loaded/unloaded) by operators and the total cycle time required was 25 seconds for both part variants. The process required cutting hexagonal holes in each rail, cutting to length, drilling, and deburring the end cut finish. Automatic changeover between part variants was required.
BOS designed a system featuring two (2) FANUC M-710iC/70 material handling robots, an operator load station, two (2) saw/drill stations, a BOS L-R laser cell, a deburr station, and an unload conveyor. The L-R cell was powered by a FANUC M-20iB robot equipped with a Laser Mechanisms FiberCut laser cutting head and an IPG YLR 2kW rackmount laser to perform the laser cutting of four (4) small and precise hexagon shaped holes into the extruded aluminum tubes.
The dual saw/drill stations were utilized to create the LH and RH parts without changeover and to optimize the system throughput by cutting both ends of the extrusion simultaneously. The first material handling robot with a dual gripper was strategically placed to move parts between the operator load, the BOS L-R cell, and the saw/drill stations. Two (2) drill spindles mounted beside the saws were programmed to be automatically activated after the saw cutting process to drill two (2) stanchion mounting holes on each end of the rails. The second material handling robot utilized a universal gripper to pick parts from either saw/drill station and place them in the deburr station.
The electric deburr station utilized a spindle with carbide filled polymer wheel to smooth the rough edges of the aluminum rails. BOS programmed the robot to compensate for the deburr tool wear over time, optimizing the equipment life without adding the cost of any passive or active compliance device.
The solution of integrating the BOS L-R into a turnkey workcell with saw/drill and deburr stations was successful due to the fact that this laser cell requires minimal engineering time for our team to deploy into an automated system. Additionally, by having integrated several laser cells on past projects, BOS has streamlined the integration costs of these systems and was able to pass these savings on to the end customer.
The dual saw/drill stations reduced the overall footprint of the system and improved part cut quality and dimensions, due to the removal of part handling operations between the saws.
The electric motor-based solution for deburring was an innovative solution compared to a pneumatic motor-based alternative because of its lower cost of operation and maintenance while significantly improving the consumable lifetime of the deburr tooling.
BOS successfully met the customer requirements regarding cycle time (25 seconds per part) and over-delivered on achieving automatic part variant changeover at the push of a button (contractual requirement was less than 60 minutes).
LEARN MORE ABOUT LASERS AND AUTOMATION
We can help you to achieve your business' goals