ASSEMBLY AUTOMATION SOLUTIONS FOR MANUFACTURING
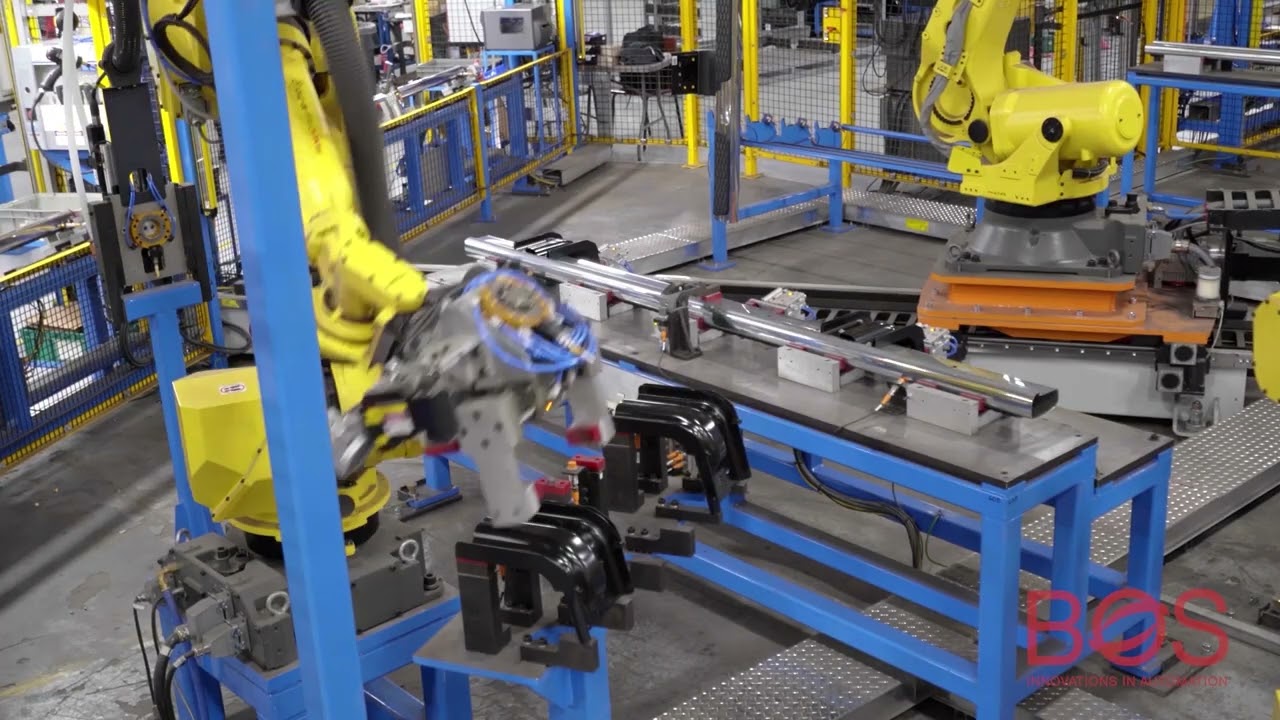
Assembly automation is the process of assembling multiple components into a final part or product as part of a manufacturing process, using automated technology such as robots to perform the sequence of operations.
The automated assembly system counts on robotic arms, sensors, vision technology and automated guided vehicles (AGVs), and can be programmed for various assembly purposes. The finished machine is an assembly cell or part of a larger assembly line.
Automating assembly processes allows manufacturers to improve productivity and quality. It can also improve safety by automating functions that are hazardous or ergonomically challenging for humans. In some cases, automating processes is necessary due to a shortage of skilled labour to support demand. Discover how automation can help your business.
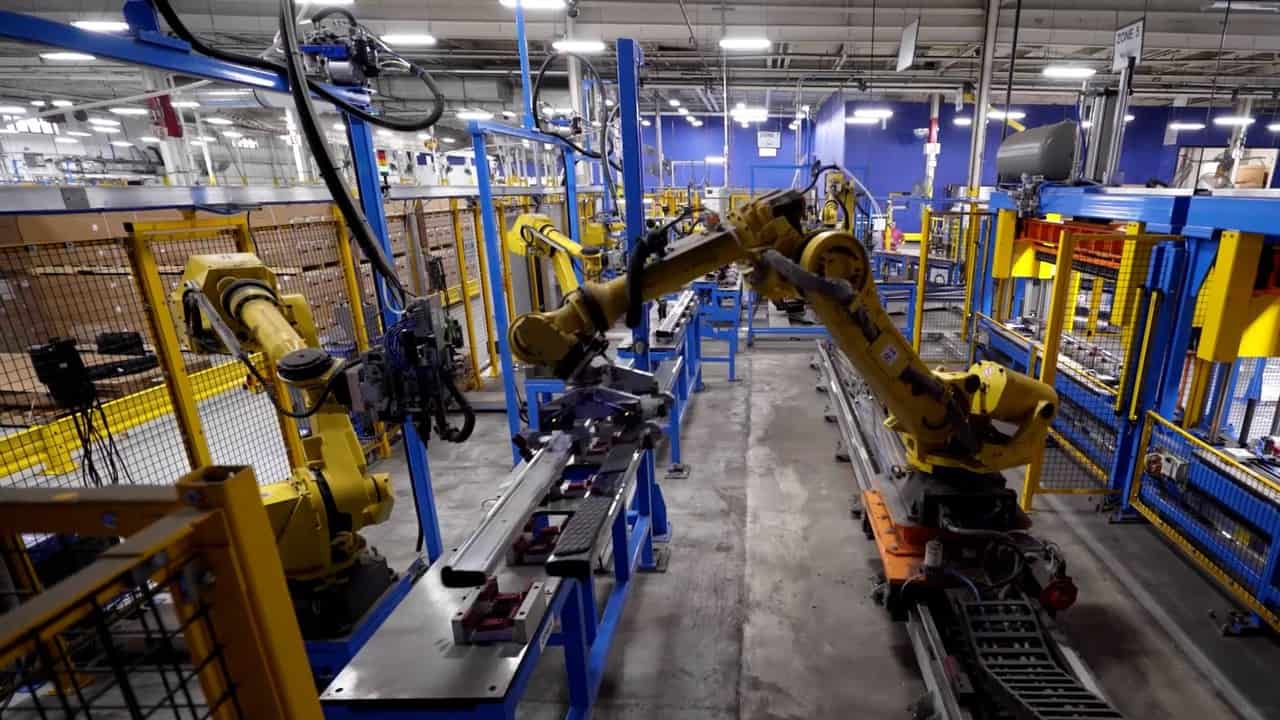
Benefits of Assembly Automation
Increase the speed and productivity of your manufacturing process
Higher quality control
Lower health and safety issues
The flexibility to respond to high variations in product types
BOS Assembly Automation Solutions
BOS was founded on Assemble & Test Automation Systems. Pallet lines, Dial Tables, Robotic Assembly, and Semi Automated Operator Stations are typical applications at BOS. Our applications team has the experience and ingenuity to find the right way to assemble and test your product.
If you require assembly for your processes with the efficiency of robotics, we’ve got you covered. With Simulation, Coordinated Motion, Collaborative robots, integration with Vision Systems and Force Control systems, BOS is on the cutting edge of what is possible with today’s Assembly Robot technologies. Integration with 3rd party systems and BOS designed hard automation are other examples on how our Robotic Assembly solutions can maximize the productivity of your business.
Robotic Assembly Cell for Truck Side Step Rails
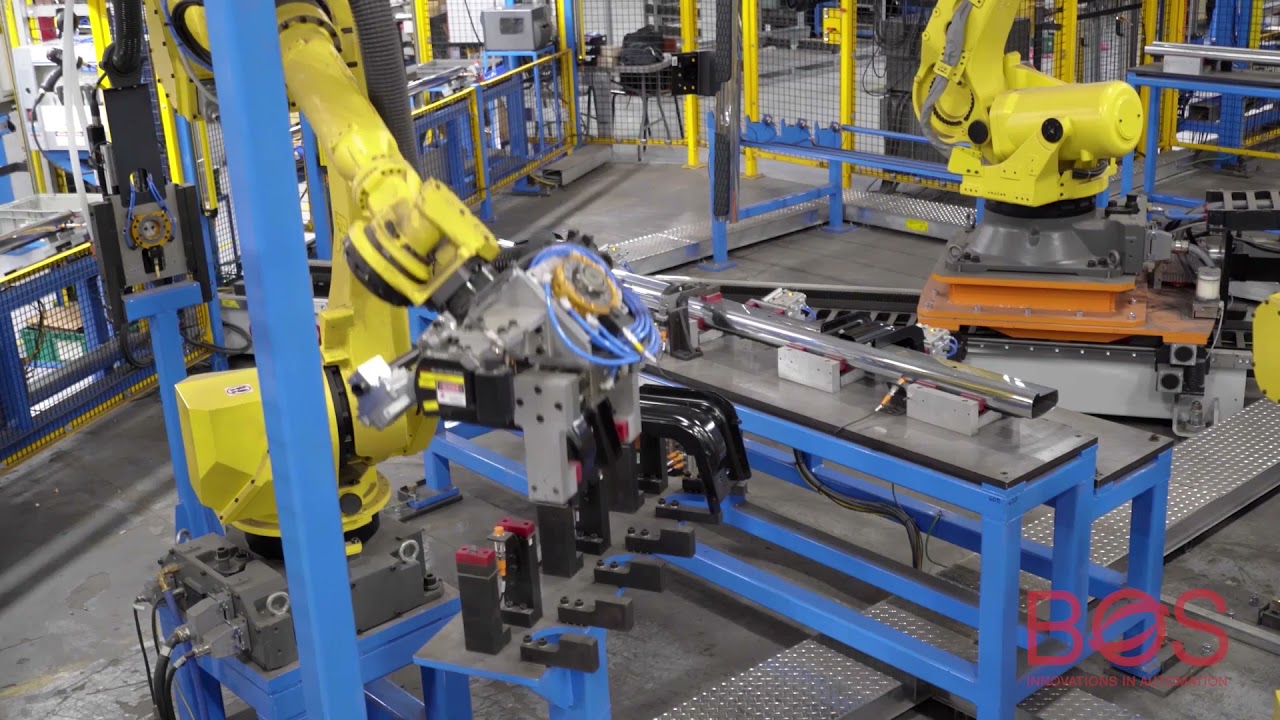
Our customer required a semi-automated robotic assembly work cell to produce stainless steel side step rails with multiple components for an OEM truck program.
There were five (5) different part variants. The machine would be manually tended (loaded/unloaded) by operators and had to achieve a part-to-part cycle time of 29 to 34 seconds, depending on part variant.
A material handling and assembly work cell featuring eight (8) FANUC robots was designed from scratch and installed at our customer’s facility. Dual end of arm tools (DEOATs) and automatic tool changing stations were deployed throughout the process to optimize the utilization of each robot and minimize the capital cost of the system.
Two (2) adjacent operator stations allowed the raw rails to be manually loaded with plastic step pads positioned in the rails. An automated press seated the pads into the rails and a Keyence 2D scanner validated that all pads were fully seated.
To accomplish the goal of attaching multiple rivnuts to laser cut holes on the rails, a 3D vision guided robotic fastening and torquing system was implemented within the work cell.
An additional operator station allowed brackets for the assembly to be manually loaded into the work cell using a dial table. The brackets were installed using another 3D vision guided robotic fastening and torquing system that automatically adjusted the position of the bracket to accommodate for variation in the position of the rail.
BOS successfully integrated multiple technologies into a turnkey solution for our customer. Using a robot transfer unit (RTU) was a concept innovation that realized reduced floor space and lowered the cost for our customer while still achieving production requirements like cycle-time.
LEARN MORE ABOUT AUTOMATION
Contact us today and see how we can help you automate your business.